Belt Filter Press
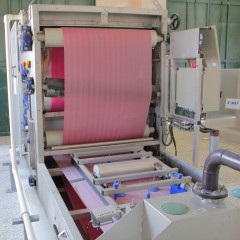
Belt Filter Press
This machine is developed to dewater sludge from different processes.there are 3 type of belt filter press :
Low pressure
Medium pressure
High pressure
The sludge is processed in three distinct stages :
• Flocculation
• Gravity drainage
• Pressing and shearing
The process begins by first conditioning the sludge. The important first step is required to agglomerate the suspended sludge solids into « flocs » and thus provide an initial separation of sludge solids from the liquid. This stage consistsin injecting polymer in the sludge. Normally, the floculant is injected upstream the sludge pump to benefit from a progressive mixing by the eccentric screw of the pump. Conditionning is also designed to build a « structure » into the sludge floc so that they can withstand gradually increasing pressure and shearing action. In general, a BFP cannot function without polymer conditionning. Then floculated sludge spreads over the filtering belt using a distribution tube in Upvc : free water created during sludge conditioning drains through the belt pores. The importance of proper sludge conditioning in BFP dewatering can be readily observed at this point. Without conditioning, liquid sludge will simply pond in the gravity drainage section or run out the edges of the belt. When the two filtering belts converge, pressing andshearing stage begin. The first roller has an important diameter (∅400) in order to get a progressive pressing. Pressing and shearing operate all along the belt length thanks to 9 rollers with a diameter of 200, which enable to get a progressive pressing of the sludge.Therefore sludge dewatering is maximal and the capture rate is optimal. After the last pressing stage, the dewatered sludgeis scraped from the filtering belts, and then evacuated on a mesh conveyor or other system. To enable the filtering belts to keep their filtration capacity, they are washed continiously on the travel back to the thickening zone. Pressing roller Gravity filtration stage Regulation bar washwater spraybar-lower belt Pressing and shearing stage Washwater spraybar upper belt Scrapper blades .
Sludge dewatering – Belt Filter Presses
OMEGA SC range
Designed for the continuous mechanical dewatering of municipal and industrial sludge in small capacities.
- Belt width : 0,60 and 1 m
- Sludge flowrate : up to 6 m3/h
- Easy maintenance and supervision
- Low energy consumption and operating costs
- Very clean operation
- Full enclosure for safety and odor extraction
- Material : stainless steel 304L, 316L or other
OMEGA 100 000 range
Designed for the continuous mechanical dewatering of municipal and industrial sludge in small and medium capacities.
- Belt width : 1 to 2 m
- Sludge flowrate: up to 12 m3/h
- Low energy consumption and operating costs
- Clean operating system
- Very clean operation
- Easy access for supervision and maintenance
- Visual control of the sludge during dewatering
- Material : stainless steel 304L, 316L or other
OMEGA 1000 range
Designed for continuous mechanical dewatering of municipal and industrial sludge in medium and big capacities.
- Belt width : 1 to 3 m
- Sludge flowrate : up to 30 m3/h
- Low energy consumption and operating costs
- Clean operating system
- Very clean operation
- Easy access for supervision and maintenance
- Visual control of the sludge during dewatering
- Material : stainless steel 304L, 316L or other